Gas Turbine Wet Compression
Nearly Instant Power Boost of up to 20%
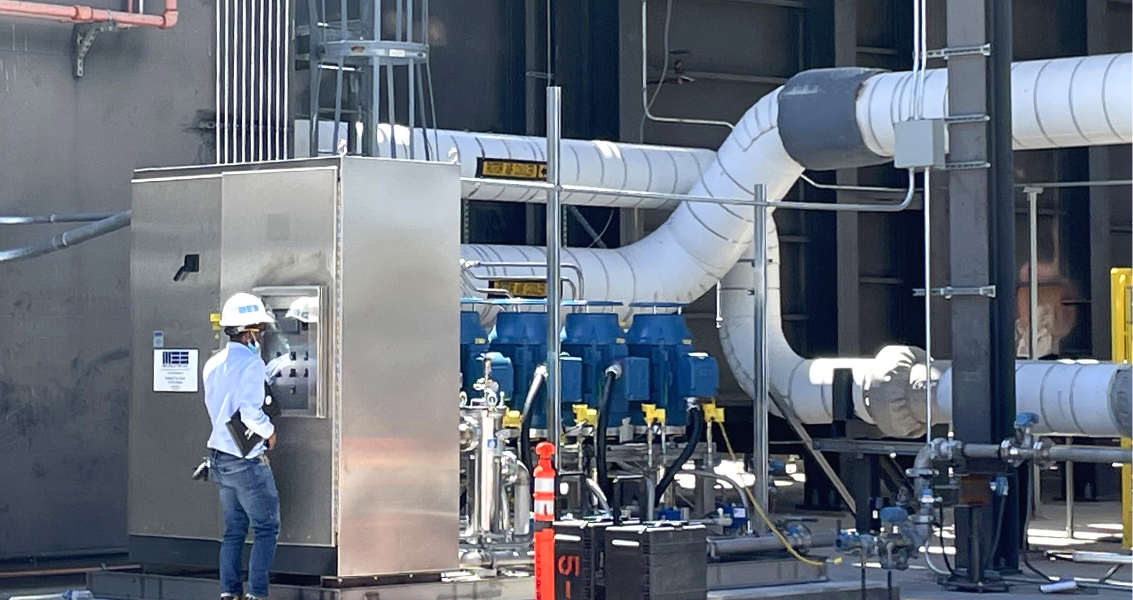
Wet compression consists of injecting pure water fog into the inlet of a gas turbine engine in order to improve output and heat rate. When the water droplets evaporate inside the compressor, they reduce the temperature and significantly reduce the work of compression, which means more power is available at the output shaft. Wet compression produces a power boost of 5% to 10% for each one-percent (of the air mass flow) of water injected.
- Droplets evaporate inside the compressor to give an evaporative intercooling effect.
- Spraying 2% of the air mass flow gives up to 20% power boost, systems have been installed that output as much as 2.5% of the air mass flow.
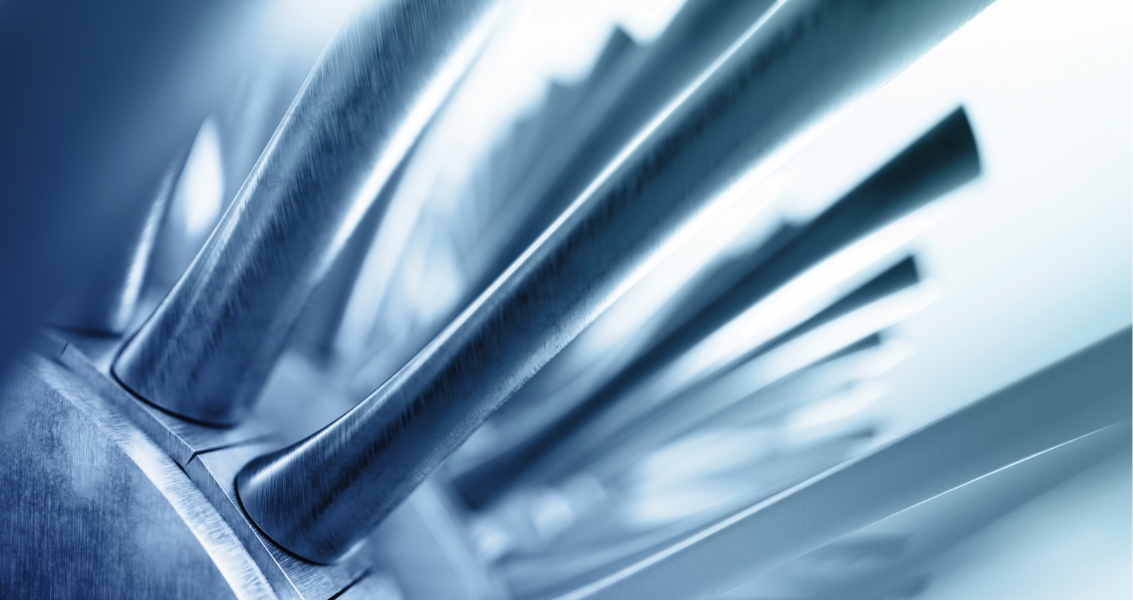
We’ll gladly supply a detailed power recovery report for your existing gas turbines including:
- Installed system cost
- Guaranteed power gain
- Predicted MW-hr gain per year
- Heat-rate improvement
MeeFog GT Installation Diagram
Click the different areas of the diagram below to learn more information about our system.
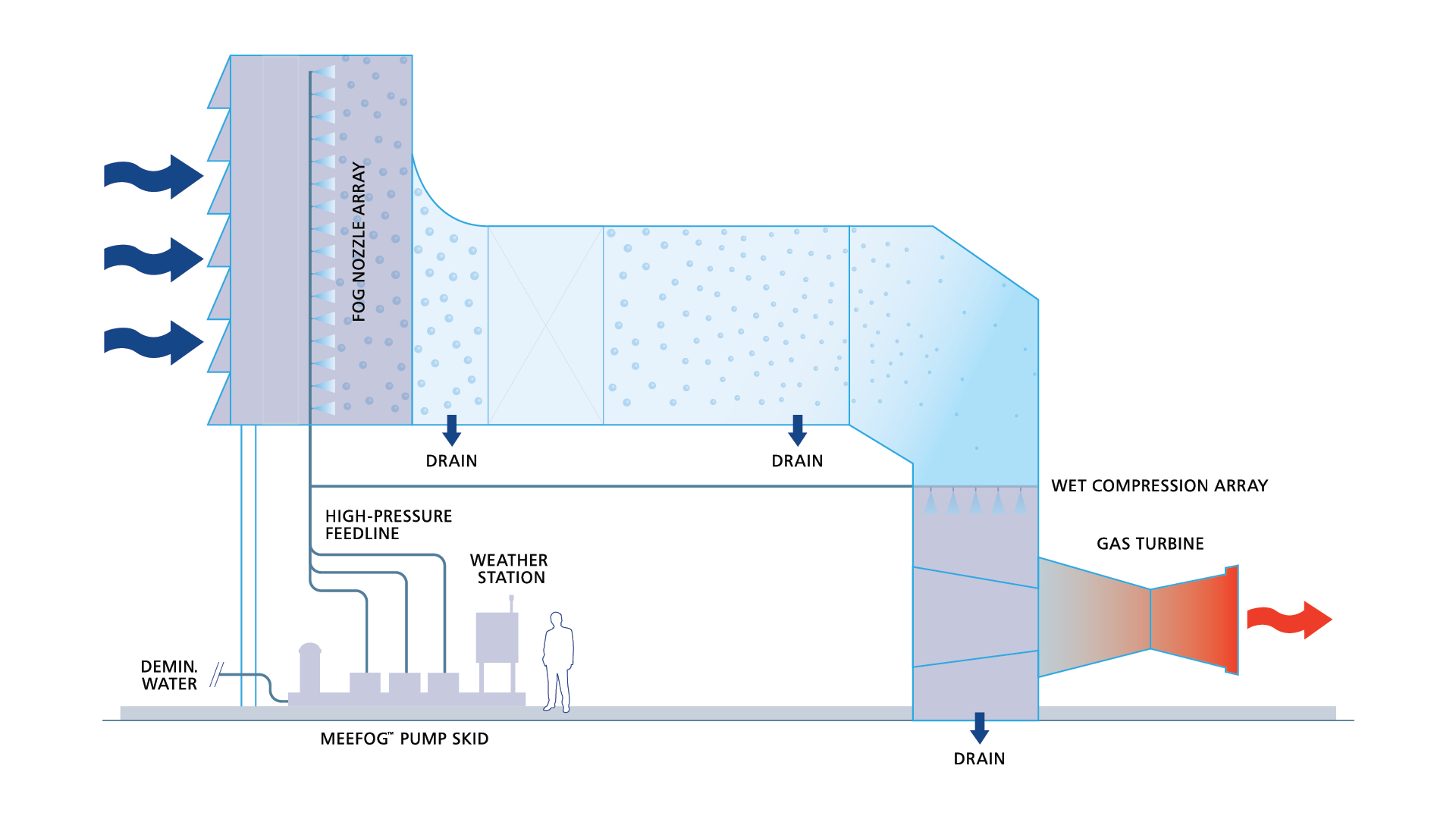
Pump Skid
Pump Skid
Stainless-steel welded frame with oversized inlet water filter. Water lubricated direct drive pumps means no oil or drive belts to change. Variable frequency drives are used to reduce flow for staging.
Evaporative Cooling Fog Nozzle Manifold
Evaporative Cooling Fog Nozzle Manifold
Cools to wet bulb temperature with droplets evaporating prior to entering compressor. Fog nozzles mounted on stainless steel tubing are wired for FOD avoidance. These precision nozzles are manufactured and tested in our own facility.
Wet Compression Nozzle Manifold
Wet Compression Nozzle Manifold
Fog droplets evaporate inside the compressor, giving an intercooling effect that reduces the work of compression. Water sprayed into the compressor will reduce NOx as well, but only about half as much as water sprayed into the combustors, because much of the air bypasses the combustion process.
SYSTEM OVERVIEW
Droplet Comparison
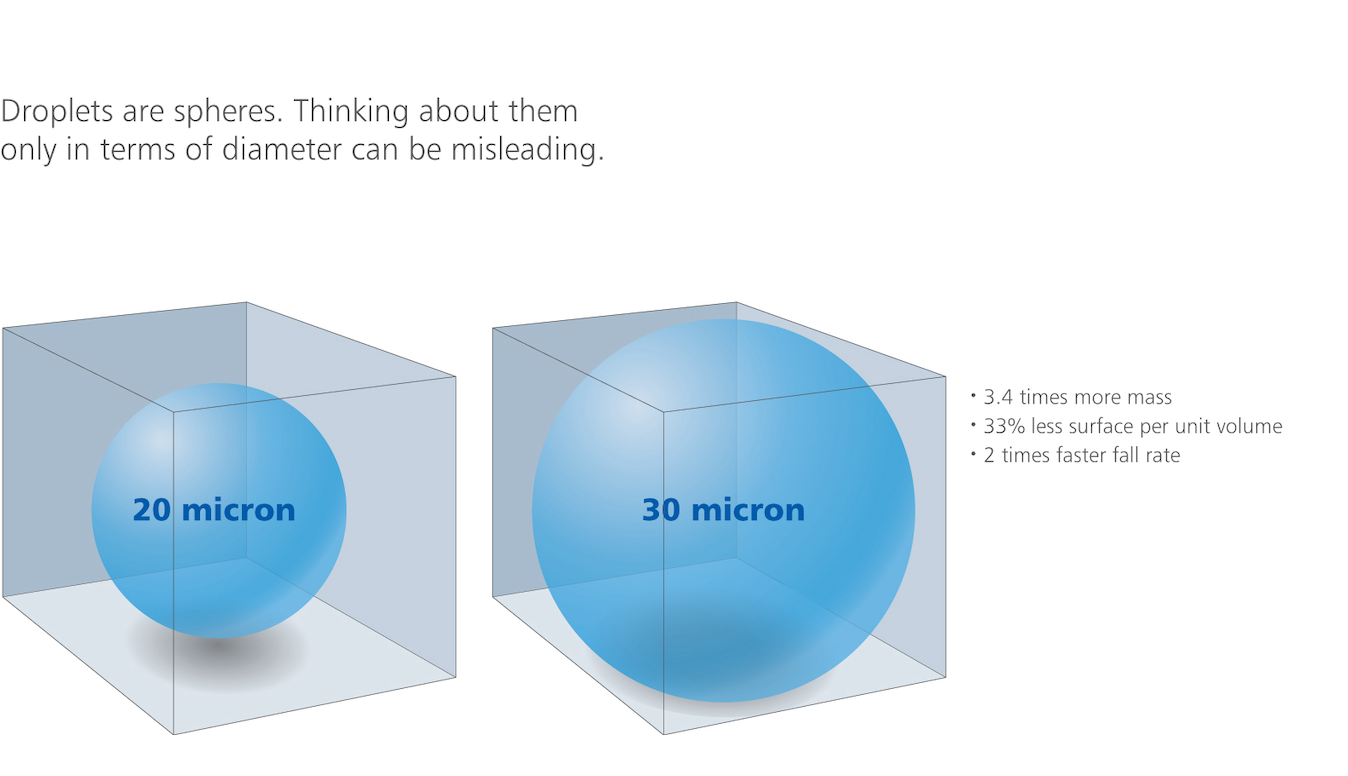
Small droplets have a larger surface to volume ratio compared to larger droplets. This allows them to evaporate much more rapidly than larger droplets.
Want Proof?
We’ll gladly supply a detailed power recovery report for your existing gas turbines including:
- Installed MeeFog system cost.
- Predicted MW-hr gain per year.
- Fuel savings.
Featured Case Study
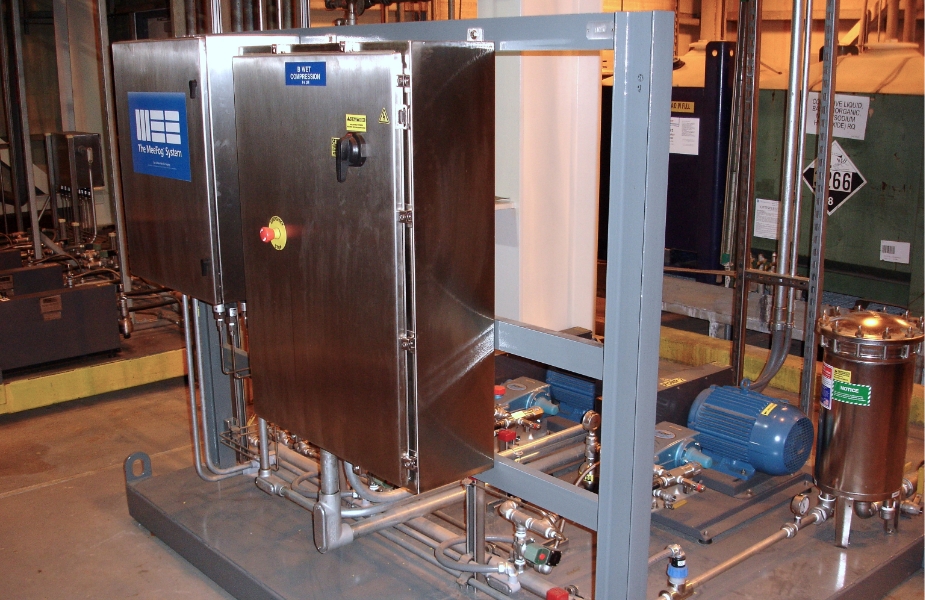
Adding Wet Compression to Existing Fog System
Eagle Point Power Generation – Westville, NJ
The Challenge
When Rockland Capital took over operating a twenty-year-old combined cycle plant, it looked for a cost effective way to get more value out of the facility.
The Solution
Adding a MeeFog wet compression to an existing MeeFog inlet cooling system to generate an additional 4 MW.
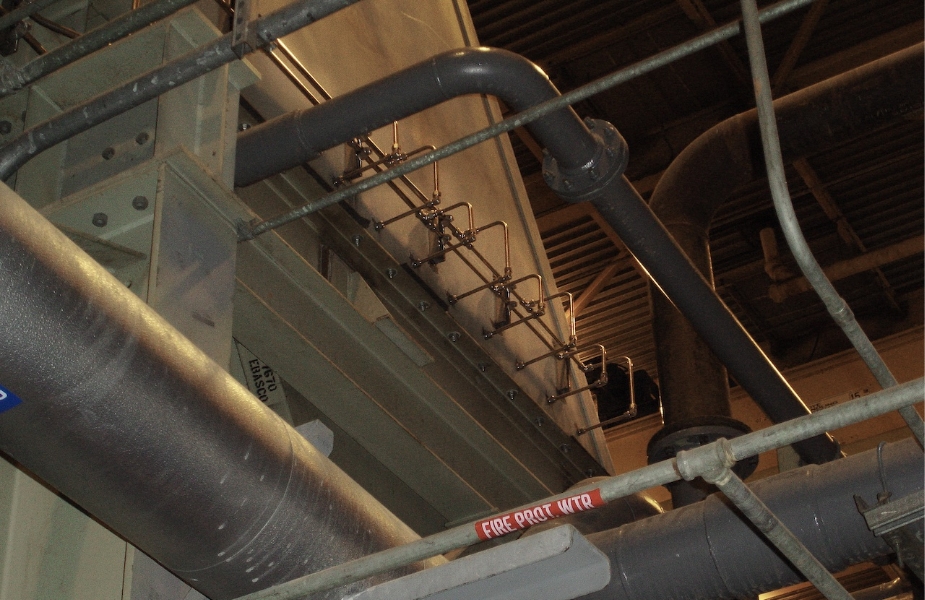
Eagle Point Power Generation (EPPG) in Westville, NJ is a 225 MW combined-cycle facility with two GE Frame 7EA turbine generators, two Nooter/Eriksen Heat Recovery Steam Generators and a single 50 MW Alstom condensing steam turbine that sells power into the PSE&G zone of the PJM market. The facility began commercial operations in 1991 as a cogen plant providing steam to the Eagle Point Refinery, but when Sunoco shut the refinery down in 2009, it switched from cogen to combined cycle mode.