How Gas Turbines Work (Combustion Turbine Working Principle)
Blog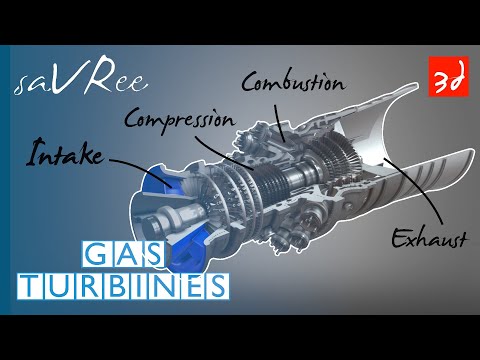
Introduction to Gas Turbines
Hi, John here. In this video, we’re going to take a look at a gas turbine, also known as a combustion turbine. I’ll show you all of the main components that are assembled to form a gas turbine. I’ll show you how it works, and then I’ll show you how a gas turbine looks when it’s installed within a power plant.
Basic Diagram and Working Principle
Before we have a look at a real gas turbine in 3D, let’s take a look at this basic diagram. If you’ve ever worked with combustion engines before, you will have heard the phrase “suck, squeeze, bang, blow” — or intake, compression, ignition, exhaust. With gas turbines, it’s very similar. We have an intake stage, a compression stage, a combustion stage, and an exhaust stage. The exhaust stage is also sometimes referred to as the expansion stage. So we have compression on the left and expansion on the right. We also have the cold section of the turbine on the left — that’s everything colored in blue — and then we have a hot section, which are the parts of the turbine that are colored yellow, orange, and red.
How a Combustion Turbine Works
I’ll tell you now briefly how a combustion turbine works, because it’s actually quite simple and quick and easy to explain. And then we’ll look at some of the components in more detail when we take a look at the 3D model. A combustion turbine ignites fuel in order to heat up air. Air is a gas, and that’s why we call this type of turbine a gas turbine. We’re not calling it a gas turbine because we are using natural gas to fire the turbine — we’re calling it a gas turbine because we’re using a fuel. It may be natural gas, it may be a light fuel oil, it may be coal dust — it may be up to about 30 different types of fuel — and we’re using that fuel, the chemical energy from the fuel, when we ignite it and burn it to heat up air. Like I say, air is a gas, so this is a gas turbine.
Gas Turbines vs. Steam Turbines
The other type of turbine that you may have seen is a steam turbine. Steam turbines require steam to operate — that’s the working fluid. Gas turbines require a gas. It may be air, but there are other gases that you can use as well. It really depends upon the system. One type of system is open, and one type is closed. In this video, we’re looking at an open type system, and that’s the only type of system that we’re going to discuss. Open type systems use air — ambient air from the surrounding environment — as the working fluid.
The Continuous Process in a Gas Turbine
So what’s happening? We’re drawing air in on the left through our air inlets. We’re compressing the air. We’re increasing its pressure, increasing its density and temperature as well. Then we’re feeding that compressed air to the combustion zone, where we ignite fuel to heat up the air. And then this hot air — this hot gas — is discharged from the combustion zone across a turbine. And as it passes over the turbine blades, the turbine blades are going to move, and that’s what’s going to cause the shaft — the central shaft — to rotate. The central shaft is connected to the compressor. All of the blades in the compression zone are referred to as the compressor. Each row of blades is referred to as a stage. So the compressor is connected to the turbine, so that when the turbine rotates in the hot section of our combustion turbine, the compressor and all of the blades there will rotate as well. This is going to cause more air to be drawn in and compressed, and then fed to our combustion zone, and the process is continuous. This type of prime mover is referred to as an internal combustion engine. The type of internal combustion engine that most people are aware of is probably the four-stroke engine or the two-stroke engine. These are the engines that you have in cars and motorbikes, etc.
Steady-Flow and Efficiency of Gas Turbines
Those types of engines, though, are intermittent. You have combustion periodically within the engine. With a gas turbine, you have constant combustion. It’s a steady-flow internal combustion engine. Because it’s a steady-flow engine, it’s actually quite efficient as well. Typical efficiencies for gas turbines are around 30 to 35%, going all the way up to 40%, maybe slightly higher for modern gas turbines. If we combine a gas turbine with a steam turbine, we can actually put that efficiency all the way up to 55%, maybe even 60%, if we’re using a very modern design and we have very modern steam and gas turbines. When we do that, we actually call that type of plant a combined cycle plant, and I’m going to show you exactly how that type of plant works towards the end of the video.
Applications of Gas Turbines
So we know now how a gas turbine works. We draw air in, we compress it, we ignite a fuel, we heat up the air, then we exhaust the air or discharge it from the combustion space across our turbine blades. Our turbine blades move, our main shaft rotates, and the process then continues. What’s interesting about gas turbines is you can use them for many different types of applications. Aircraft engines are essentially gas turbines. They have a very high power-to-weight ratio, and that’s what makes them ideal for usage in the airline industry, where weight has to be reduced as much as possible in order that the aircraft can take off.
In the power generation industry, we take a gas turbine and modify it slightly so that instead of just discharging the hot air directly out to atmosphere, we can instead perhaps reclaim some of that heat to make our turbine more efficient. And we can connect the central shaft—the single shaft of the turbine—to a generator. The generator rotor will rotate, and we will generate electricity.
Types of Gas Turbines: Heavy Frame and Aero-Derivative
Now, there are different types of gas turbine that are available to us. Heavy frame and aero-derivative are the two that you’re likely to encounter. But it’s the heavy frame design that allows us to reach megawatt capacities in excess of 250 MW. The aero-derivative design is mostly used within the aircraft industry, although it is used for power generation applications as well, and it’s essentially a streamlined version of the heavy frame design.
Characteristics and Comparison of Turbine Types
So, heavy frame design is used for large power generation requirements where we want a lot of electricity. It’s well suited to the power and energy industries. And then there is the aero-derivative design, which is like the slimline version which we use in the aircraft industry and also for minor or smaller power generation applications.
If we take a look at this diagram here, you can see that we’ve got two main gas turbine designs: aero-derivative and heavy frame. The power output for the aero-derivative type gas turbines is in the range of about 30 to 60 MW—that’s electrical power—whereas the heavy frame design is within the 200 to 500 MW range. In terms of efficiency, they’re quite similar. Aero-derivatives have an efficiency of about 39 to 43%, and the heavy frame design will be in the range of 37 to 40%. Actually, I think that’s quite high. I think it would be more in the range typically of about 35 to 37%. If we were to combine those types of turbines with steam turbines and we get what’s called a combined cycle power plant, then the efficiency increases, as you can see, to over 50% for both types of turbine. That’s a significant increase.
A Look at a Real Gas Turbine and Its Components
Let’s now take a look at a real gas turbine and all of its components, and then we’ll take a look at a combined cycle power plant.
So, here is our gas turbine. This is how it would look if you were looking at it in the field. It normally would actually just sit within a box. Depending upon the size of the turbine, the box can be quite small, or it may be quite large, and you can get in there and comfortably walk around. It may be air-cooled; it may be water-cooled. It depends upon the design. It will have a control oil system installed nearby. Quite often, the control oil system tank will be mounted directly underneath the turbine—so, in this section here where my mouse is—and then we’ll have several pumps that we use in order that we can pump the control oil around the system. And we’ll use it to actuate valves and move actuation pistons, etc. The gas turbine itself is relatively simple in terms of concept, although there is a lot of engineering that goes into it. We draw the air in on the left. You can see where the air is being drawn in; it’s indicated in blue. You can see our central shaft as well—it’s this item here that’s going to connect to our generator.
We draw the air in; it flows past a series of compressor blades, and we’re going to increase the pressure as the air moves across each of these blades. And remember that each row of blades is called a stage. So every stage, as we move from left to right, we’re going to increase the air pressure and, correspondingly, the temperature as well. For heavy frame gas turbine designs, you’ll be looking at compression ratios of about 15, maybe up to 18:1. So, from here on the left over to here, all the way on the right where my mouse is, where the air is discharged, the compression ratio will be up to 18:1. With aero-derivative engines, it’s actually higher—it might be 30:1. Those types of gas turbine are more focused on generating thrust, compared to the heavy frame design where we’re focused on generating electrical power—or at least that is our end goal. Aircrafts require thrust in order to stay up in the air. Power plants require as much power as possible in order to be profitable.
So, we take the air. It’s discharged through these two channels, and then we reach our combustion zone. We’re going to inject fuel into this space. The fuel’s going to be injected here. We ignite the fuel, we get combustion, we get heat, and we use the heat to heat up the air. We go up to the top here—you can also have a look from the top. You can see the fuel lines coming along here, my mouse is also along here and along here, and the two on the bottom. And that fuel then is going to be sprayed and discharged into the combustion space.
Initially, we’re going to need to have a spark in order to ignite the fuel. But once the gas turbine is up to speed—typically beyond 50%—the temperature of the air is enough that we can keep combustion constant, and we don’t need any external ignition source, for example, from a spark plug or similar. The hot air that’s being heated is then going to be discharged through nozzles—through these here. The nozzles are stationary, and we pass the hot air across the blades of our turbine. See here is one set, here’s the next set, and here is the next set.
Those turbine blades will rotate, the central shaft will rotate, and we can connect the central shaft to the generator to generate electricity. When we discharge the hot air at this end here, it may be 500, maybe 550, 600°C in extreme cases. And that’s quite a lot of energy that we’re going to discharge—just potentially straight to atmosphere out through this hole. So, rather than do that, what we can do instead is connect the gas turbine to a steam system. This will increase the overall plant efficiency.
Combined Cycle Power Plants
Here is a combined cycle power plant. We call it a combined cycle power plant because gas turbines use what’s called the Brayton cycle. The Brayton cycle is a type of thermodynamic cycle. The other type of cycle that you’ll see when looking at steam turbines is the Rankine cycle. Each of these cycles is named after the person who invented them. In engineering, you’ll also see the Otto thermodynamic cycle and the Diesel thermodynamic cycle. They’re all just describing different types of thermodynamic process.
Because we’re using a gas turbine that is housed within this box here, and the steam turbine is housed over here within one type of power plant, we’re essentially using a Brayton cycle and the Rankine cycle together, and that’s why we call this type of power plant a combined cycle power plant. Very briefly, I’ll explain to you how it works. We’ve got our gas turbine here. It connects on a shaft to a generator, which is housed within this box. And then we have three phases of power which are coming out here. They join to a transformer, and then we send that electrical power to our consumers. We draw air in through these filters here, and the air will pass through a series of filters before it gets to our gas turbine. We filter the air because we don’t want any foreign particles being sucked into the turbine, because that might damage our compressor blades or our turbine blades. So it’s important to filter the air. It’s also important to de-ice the air to make sure no water or moisture is sucked into the turbine.
Those hot exhaust gases—remember they may be at 500°C or 550°C, etc.—will be discharged along here and into what’s called a heat recovery steam generator, which is a type of boiler. And as the exhaust gases move from left to right along here, they transfer their heat to water, and then the water turns to steam. At this point, the hot gases—the exhaust gases—can be discharged through this hole and to atmosphere. The steam from the heat recovery steam generator is sent to the steam turbine, and then the steam turbine rotor rotates, and we generate electricity through our generator here.
So, one heat source which is used to operate both a gas turbine and a steam turbine. When we do that, we have a combined cycle plant, and we increase our efficiency—for example, from about 35%, potentially all the way up to 50, 55, and maybe even 60%. If you want to use any of the 3D models shown in this video, then head on over to sa.com. We’ve got over 400 engineering 3D models that you can use directly through a web browser in AR or VR.
If you want to learn more about engineering, we’ve got over 45 hours of engineering video tutorials and courses at savy.com, and you can learn about valves, pumps, power stations, electrical transformers, and many other common engineering machines and processes.
Before you go, don’t forget to subscribe to the YouTube channel. Thank you very much for your time!