Maximizing Power Output with MeeFog Systems at Tuxpan Power Plant, Mexico
Gas Turbine Wet Compression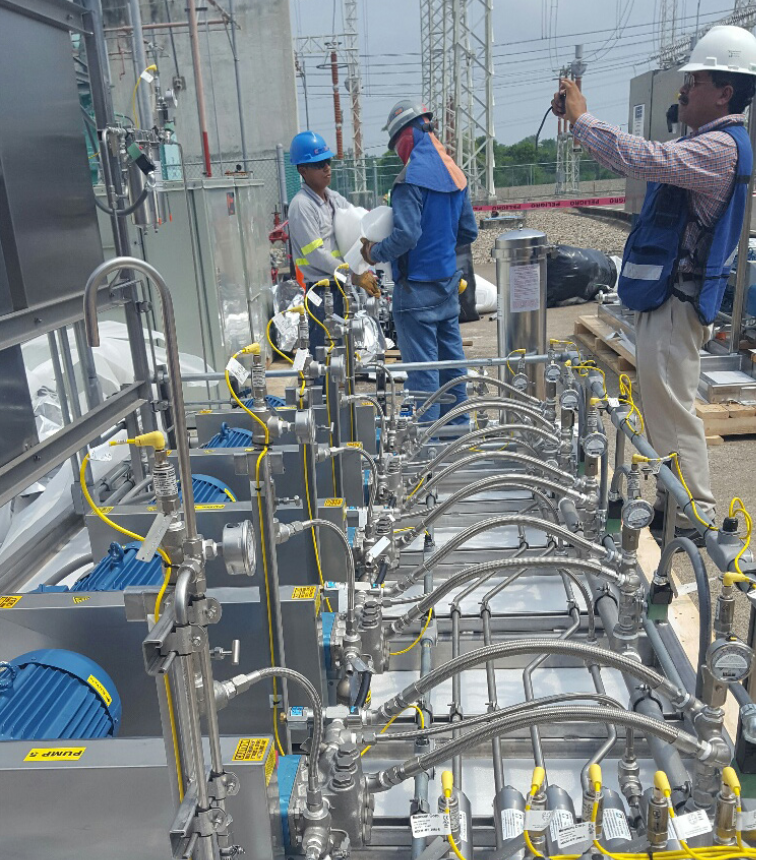
Global Power Generation
The Tuxpan III and IV combined cycle power plant is operated by Global Power Generation (GPG), a subsidiary of the Naturgy group, and is one of the largest combined cycle plants in Mexico. Located northeast of Mexico City in Veracruz, the plant consists of two identical power blocks. Each block includes two MHPS 501F gas turbines, two heat recovery steam generators, and one steam turbine. Each block generates approximately 500 MW, bringing the plant’s total capacity to 1,000 MW. In 2017, Tuxpan III and IV Combined Cycle Plant fitted its four MHPS 501F gas turbines with MeeFog Wet Compression. This increased output per turbine from 164 MW to 180 MW. Seven years later,the turbines and their wet compression systems are still going strong. A detailed inspection in 2024 revealed no blade erosion or other damage or increased wear on any of the gas turbines. Initially, the Tuxpan plant utilized media-type evaporative coolers for turbine cooling, but as demand for power increased, the need for greater efficiency and power output became evident. To address the rising demand for electricity in a competitive, liberalized energy market, the plant sought an effective solution to boost power without compromising performance or increasing wear and tear.
Challenges Faced:
With new energy regulations in Mexico allowing power to be sold directly to end users, providers seeking to capitalize on this market opportunity must deliver the maximum amount of electricity at the lowest possible cost. Before the installation of the MeeFog Wet Compression system, each MHPS 501F turbine at Tuxpan produced 164.2 MW. The facility faced the dual challenge of increasing output to remain competitive while keeping operational costs low and maintaining turbine integrity. In this highly competitive market, the Tuxpan plant needed a solution that would increase turbine efficiency without adding significant costs or risking damage to the turbines. Conventional methods, such as increasing fuel input or operating the turbines at higher temperatures, could lead to increased maintenance requirements and premature equipment failure.
Solution:
To boost power output and operational efficiency, Tuxpan III and IV power plant turned to MeeFog once again, its four M501F2 gas turbines with MeeFog wet compression systems, increasing the output per turbine from 164 MW to 180 MW. The key elements of the installation include:
- Two fog pump skids at each gas turbine.
- Fog nozzle manifolds in the inlet.
- A 14-stage fog spray system, with each stage consisting of 71 fog nozzles, totaling 994 nozzles.
The 14 stages of wet compression are tied into the gas turbine controls so the grid authority has control over the amount of power augmentation via the automatic generation signal. This allows for seamless control of the amount of power augmentation above base load as required by the grid authority.
Installation Specifications:
The Tuxpan combined cycle plant had media type evaporative coolers installed on each of the Mitsubishi Hitachi Power Systems (MHPS) 501F2 gas turbines. The MeeFog systems were installed downstream of the existing evaporative media. The nozzle manifolds deliver a few degrees of evaporative cooling as the media-type evaporative coolers are not 100% effective. They also deliver additional wet compression spray with a flow rate equal to 1% of the air mass flow of the gas turbines. Mee Industries provided turnkey installation of the wet compression systems including connection to water and electrical supplies. General Electric provided controls modifications with support from Mee’s engineers.
System Upgrade:
- Installed two fog pump skids per turbine and fog nozzle manifolds in the intake ducts.
- Designed a custom solution featuring 14 stages of fog spray output to fine-tune cooling performance based on real-time demands.
- Integrated the fog system with existing turbine controls to allow dynamic adjustment of wet compression levels.
Testing and Validation:
- Following seven years of operation with over 20,000 operational hours per turbine, the turbines were subjected to detailed inspections in 2024.
- Inspections revealed no signs of blade erosion, corrosion, or other damage, confirming the long-term durability and effectiveness of the MeeFog system.
Operational Integration:
- The MeeFog system was seamlessly integrated into the turbine’s existing controls, enabling real-time dynamic adjustments based on power demand.
- The system provided enhanced operational flexibility and improved the plant’s responsiveness to grid demands.
Results:
The success of this project highlights the viability of Wet Compression as a reliable and efficient method for enhancing turbine performance. With over 82,000 hours of operation and no signs of turbine damage, the system has proven to be both safe and durable, offering a sustainable solution for power plants looking to increase efficiency without compromising on equipment life.
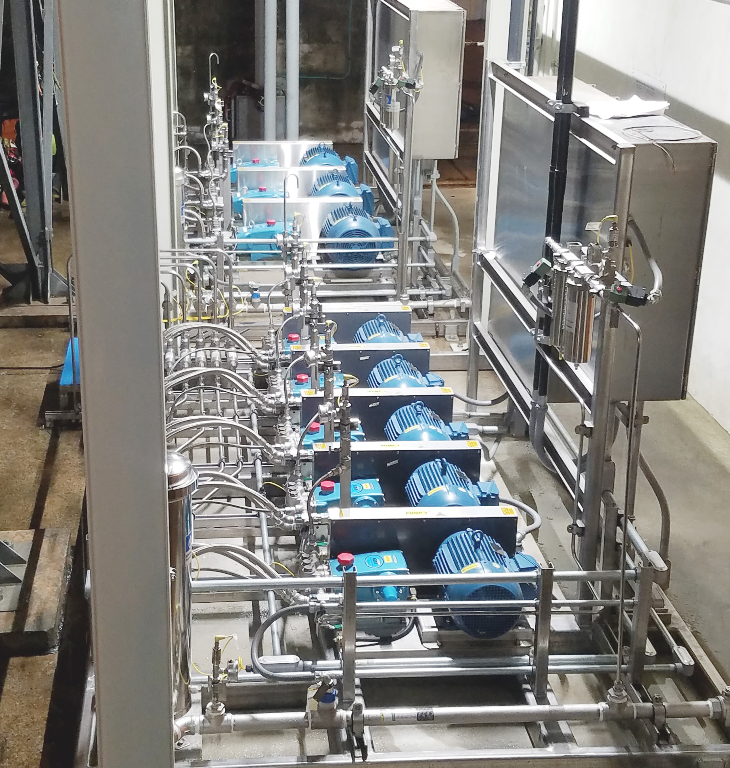
Client Benefits using MeeFog Technology:
- Increased Power Output:
Each turbine’s power output increased by 16 MW, contributing an additional 64 MW to the plant’s total capacity, improving overall grid stability and responsiveness. - Enhanced Operational Efficiency:
After extensive use, the turbines maintained their optimal performance, demonstrating that the MeeFog Wet Compression system significantly improves turbine efficiency while preserving the integrity of critical components. - Sustainability & Environmental Impact:
The system also contributed to reduced NOx emissions and improved fuel efficiency, supporting the plant’s sustainability goals. The wet compression technology allowed the turbines to operate with a lower environmental footprint while increasing energy production.
“The system produces 16 MW of power augmentation per turbine, after 82,810 hours of wet compression across four turbines, there are no reports of any erosion or any issues with compressor blade damage.” Rafael Garcia, technical consultant for GARPE, S.A. de C.V. of Mexico.
Resources:
Discover how our wet compression systems can boost performance and lower emissions.
Contact Us:
Ready to enhance your power plant’s efficiency with MeeFog’s wet compression systems?