Watson Cogeneration Boosts Output by 10 MW with MeeFog Wet Compression System
Gas Turbine Wet Compression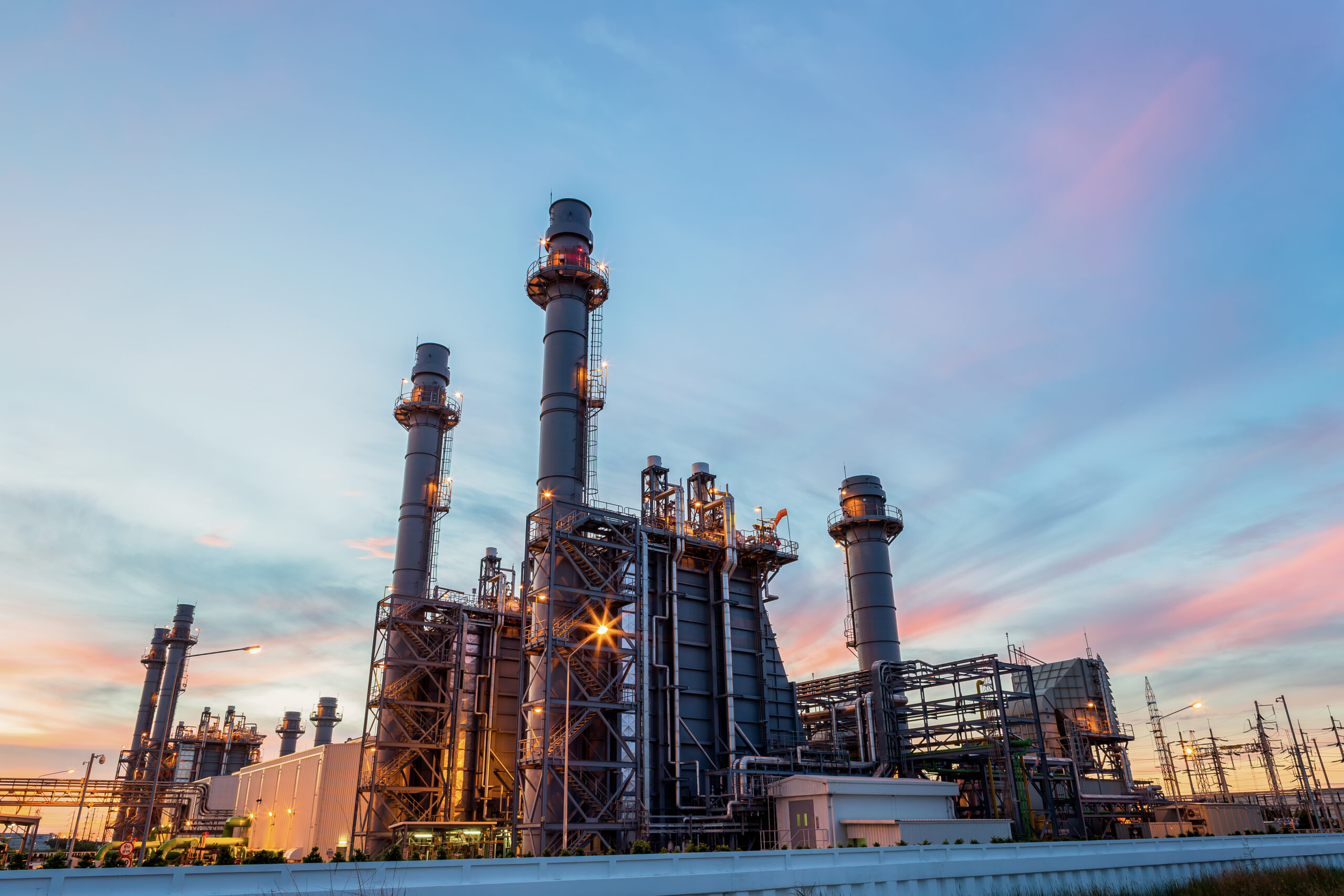
Los Angeles County, California
The Watson Cogeneration Plant (WCP) is a prominent 425-megawatt combined-cycle cogeneration facility situated on 21.7 acres adjacent to the Carson Refinery—the largest refinery in California, with a processing capacity of 365,000 barrels per day. WCP plays a crucial role in supporting the adjacent refinery by providing both high-pressure steam and electricity, while also supplying electricity to the grid.
Located in Carson, an industrial zone about 15 miles south of downtown Los Angeles, the plant is co-owned by Marathon Petroleum and NRG Energy. It supplies the Carson Refinery with high-pressure steam and electricity, critical to the refinery’s operations, which include the production of gasoline, diesel, jet fuel, and anode-grade coke. As a byproduct, the facility also produces the fuel gas that powers Watson Cogen’s turbines.
The cogeneration plant utilizes four natural gas-fired GE 7EA turbines, each rated at 83.5 MW (ISO). The exhaust gases from these turbines feed a duct-fired heat recovery steam generator, which produces both high and medium-pressure steam. Approximately half of the high-pressure steam is directed to the refinery, while the remainder is sent to two Dresser Rand steam turbines powering electric generators. Upgrades to the facility have increased its output from an initial level of 385 MW to its current capacity of 425 MW.
Challenge:
Watson Cogeneration needed to increase power output from its four existing GE Frame 7EA turbines without compromising system integrity or increasing emissions.
Solution:
The MeeFog system was utilized for wet compression, leading to an average increase in power output per gas turbine unit of around 2.5 MW, totaling to 10 MW for the entire plant. Additionally, measurements taken at the top of the stack indicated a 7 ppm reduction in NOx levels.MeeFog’s wet compression system allowed Watson Cogeneration to inject excess fog into the air stream, resulting in a 10 MW boost in power and a 7 ppm reduction in NOx emissions, all while maintaining long-term efficiency and reliability.
Installation Specifications:
The MeeFog™ system consists of a pump skid and a nozzle array connected by a latticework of stainless steel tubing. On the skid is a pump to pressurize the water to 2,000 psi, a weather station and a programmable logic controller. Within the inlet air duct and upstream of the silencers and trash screen is an array of 360 x 0.006-inch diameter stainless steel impaction pin nozzles designed to atomize the water into droplets of less than 20 microns each for rapid evaporation. This array produces up to 16.2 gpm of fog, which represents 0.35 percent of mass flow used for wet compression.
Results:
MeeFog’s wet compression system allowed Watson Cogeneration to inject excess fog into the air stream, resulting in a 10 MW boost in power and a 7 ppm reduction in NOx emissions, all while maintaining long-term efficiency and reliability.
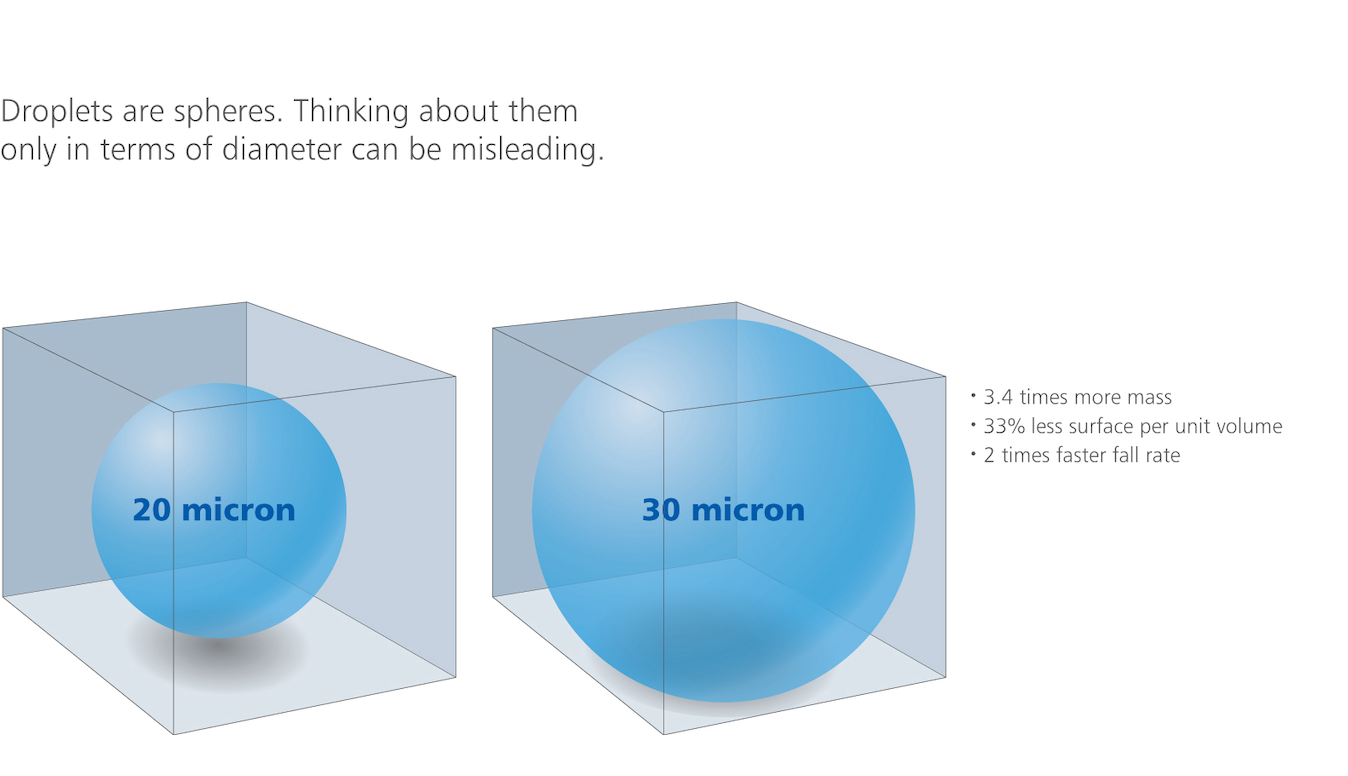
Client Benefits using MeeFog Technology:
- No fog-related blade erosion for twenty years
- 10 MW of additional capacity
- NOX emissions lowered by 7 ppm.
“We are probably the longest running wet compression user in the world in terms of total hours, having successfully used wet compression. We run the MeeFog system round the clock during the peak period of electricity generation. During more than twenty years of operation, the MeeFog wet compression system has not caused blade erosion.” -Steve Ingistov, Watson Cogeneration’s Principal Engineer
Resources:
Discover how our wet compression systems can boost performance and lower emissions.
Contact Us:
Ready to enhance your power plant’s efficiency with MeeFog’s wet compression systems?