20 MW of Power Recovery at Load-Following Power Plant
Fog Cooling For Gas Turbines & Heat Exchangers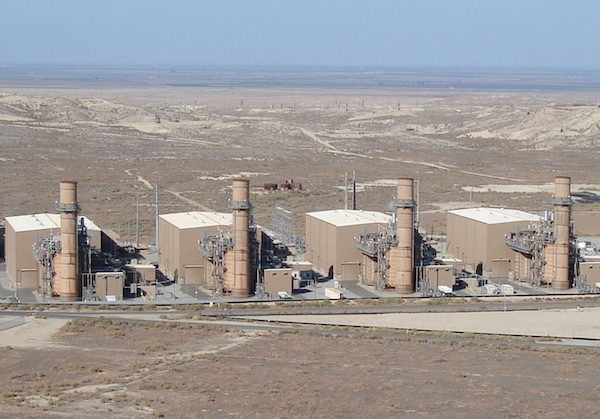
Load Following with MeeFog
La Paloma has four 250 MW ABB GT24-B combustion turbines coupled with the KA24-1 ICS combined cycle equipment. Unlike most U.S. plants, all the major equipment came from Europe: the GT from Switzerland, the steam turbines from Sweden, the generators from Germany, the steam train gearbox from France and the SSS Clutches between the generator and steam turbine from England.
Unlike most U.S. plants, all the major equipment came from Europe: the GT from Switzerland, the steam turbines from Sweden, the generators from Germany, the steam train gearbox from France, and the SSS Clutches between the generator and steam turbine from England.
“The footprint is very small considering that we produce 1000MW,” explains Pablo Cortes Oseguera, Engineering and Maintenance Manager for La Paloma Generating Company (LPGC). “The single shaft design makes the power blocks very compact.”
Another major advantage of the GT24 is the dual-combustor, sequential combustion design, which produces a heat rate in the high 6000s or low 7000s, depending on operating conditions and results in very low emissions. The NOx is controlled for 1.5 PPM, following California regulations, with the CO required to remain below 10 PPM throughout the operating range of 150 to 250 MW. The GT24s produce a minute fraction of that amount, about 0.1 PPM. Additionally, the units inject some of the HP steam into the GT combustor. This action is not to control NOx, as is done with GE units, but to increase output by about 15-19 MW net per unit, after taking into consideration the steam turbine losses.
Many people wish they could maintain the strength and stamina of their twenties. For plant equipment, however, that decline happens much sooner.
“After a few years, machines start deteriorating and become less efficient over time,” says Cortes. “Even though you do major overhauls and replace the blades and combustors, after a while your machine just isn’t performing as well as it used to.”
Challenge:
Over time, the efficiency of La Paloma’s gas turbines declined, reducing power output, especially during hot days. The plant needed to meet power demands without resorting to costly internal upgrades or full reliance on evaporative coolers.
Solution:
MeeFog Industries provided an innovative solution by installing fogging systems that could work in tandem with the existing evaporative coolers. This system allowed for precise control over cooling and power output, making it possible to dial in the exact amount of additional power needed.
Specifications:
In 2010, La Paloma underwent a change in ownership, who were interested in bringing the plant back up to its originally permitted output. One option was to upgrade the GT internals with new components from Alstom Power, but this would cost millions of dollars.
So the company decided to first pursue the more cost-effective option of enhancing inlet conditions. Although they already had evaporative inlet coolers that provided 10-12 MW of recovery, the company wanted to investigate the use of a MeeFog inlet cooling system on top of the evaporative coolers.
La Paloma provided Mee Industries with the technical information on how the plant operates and the efficiency of the turbines in the summer with the evap coolers in use. Mee conducted calculations to determine how much power a MeeFog system could recover. When Mee presented its data and provided a price for the system, the owners were interested. There was no doubt going into the project that it would be far more economical to use fogging rather than upgrading the turbine.
“I can do physical modifications to the machine which will give us more power, but they will pay millions of dollars for that,” says Cortes. “Or we can skip doing the major changes on the GT internals, just improve the intake conditions and recover an extra 5 to 6 MW. Fogging turned to be really, really good in terms of dollars per kW. It made a lot of sense to our owners.”
The Installation:
In December 2012, LPGC submitted a request to the local environmental authority (San Joaquin Valley Air Pollution Control District), requesting authority to install the foggers, stating that: “the purpose of the proposed foggers is to recover lost generating capacity on hot days when the combustion turbines are not able to operate at their full firing rate. By providing additional inlet air cooling and additional mass, beyond what the existing evaporative coolers can provide, the foggers will enable each combined-cycle turbine generator unit to achieve up to 8 megawatts (MW) of additional electrical generating capacity on hot days.” The following month it submitted a petition to the California Energy Commission, and upon approval, the MeeFog units were installed during the spring outage.
Each of the MeeFog systems at La Paloma includes a pump skid with six positive displacement pumps along with a weather station and programmable logic controller. A fogging array with 700 nozzles was installed just upstream from the inlet flange. The systems have eleven cooling stages, each providing close to 2°F of cooling.
The original plans called for the MeeFog systems to supplement the evaps when the temperatures exceeded 90° F. Once they were in use, however, this changed with the MeeFog system becoming the primary cooling source. To begin with, Cortes says, they realized that the MeeFog system uses considerably less water than the evaps, something which is especially important currently given California’s drought conditions. But the main difference is the level of control that they provide.
With the evap, if I turn it on, I know I should gain 10-12 MW power output on top of what I am making, but if turn it off I lose it all,” says Cortes. “With the MeeFog system, I can turn it on stage by stage and dial in the power boost a MW at a time based on what I need to generate. If my dispatch says you have to give me 255 MW, and I am at 250 MW, I can just turn on the fogging stages I need instead of having to run the evaporative cooler all the time.
When there is enough demand, or high enough temperature, to use the evap’s full capacity, the MeeFog system would initially be shut down. Then, if dispatch calls for additional generation, or the ambient temperature rises, the appropriate number of fogging stages would be brought on line.
“If I am in the middle of summer and power demand is very high, the gas turbine is maxed out, then I will turn on my evap coolers which will give me an average of 10-12 more MW per unit,” says Cortes. “Then if more power is needed I can turn on the Mee system and it will give me 5 more MW. I probably can recover 20 more MW out of the gas turbines if run them together.”
Learn More About Meefog Systems
Read about the benefits of Meefog’s Fog Cooling System from previous successful installations: