Las Vegas Cogen Slashes Cooling Costs and Boosts Output by 5 MW with MeeFog Technology
Gas Turbine Inlet Air Cooling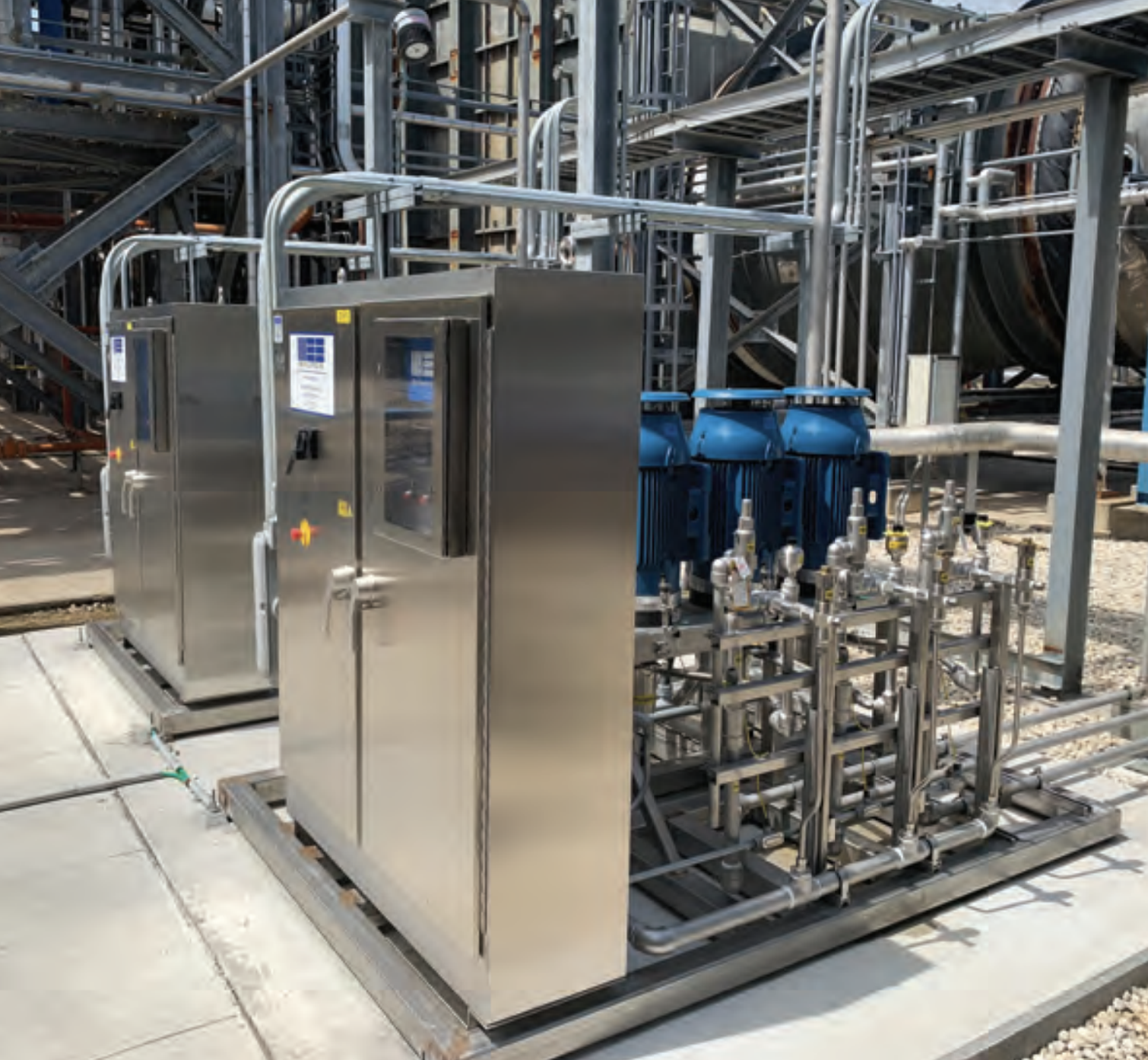
Las Vegas Cogen
Las Vegas Cogen is a GE LM 6000-based peaking plant that starts up hundreds of times per year. The electricity produced by this facility is sold to Nevada Power. In addition to generating electricity, the plant also provides thermal energy to heat a 12-acre hydroponic greenhouse. owned by the company. Given the hot and dry climate of Nevada, the plant faces very hot temperatures during the long summer months. To maximize output, the facility uses a chiller system. However, plant operators found they couldn’t cool inlet air to the dew point during periods of high ambient temperature. As a solution, a fog system was installed upstream of the chiller coil to act as a pre-cooler.
Challenge:
To limit the usage of the existing chiller system to control overall cooling costs while maximizing turbine output during peaking operations.
Solution:
Installing MeeFog’s high-pressure fogging units upstream of the chiller coil and air filters. Operate the fog units for power augmentation when temperatures are below 70°F and also use them as pre-cooling for the chiller when temperatures exceed 100°F.
Installation Specifications:
As well as being upstream of the chiller coil, the fog system was positioned upstream of the air filters. The main advantage of this positioning was that installation could be accomplished without outage time.
“As it takes time for our chillers to get online, we also use high-pressure inlet fogging of demineralized water to achieve maximum power right away,” said RD Dawkins, Operations Supervisor, Las Vegas Cogen. “We use fog exclusively when we first start our combustion turbine and also when it’s below 70 degrees outside. Above that, we also bring on a steam absorption chiller in combination, and the fogging system eliminates the need for a second chiller.”
The fog system consists of 240 nozzles installed in three stages. Operating pressure is 2,000 psi, fog water flow rate is 10.8 gpm and a total of three 5 hp high-pressure pump units were installed. Pressure drop associated with the fog nozzle manifold was nominal. The existing heating coil and pad-type pre-filters were used as fog droplet filters to remove any unevaporated fog. Although this prevented wetting of the primary air filters, water collected on the cooling coil and pre-filter and was drained off, reducing the amount of cooling accomplished by the fog system.
“The MeeFog system is low maintenance and very reliable,” said Dawkins. “Even though our fog system is upsteam of the filters, our final barrier filters remain dry and the filters stay cleaner due to the scrubbing effects of the fog.”
Results:
Las Vegas Cogen found it far more economical to exclusively use fog under certain conditions. When the outside temperature is below 70°F fog alone is used for cooling. If temperatures rise above 70°F, the steam absorption chiller is used exclusively. But because it takes time for the chillers to come on-line, the cogen facility uses high-pressure inlet fogging to provide maximum power instantly. And again as a precooler to augment the chiller when ambient temperatures exceed 100°F. Although the fog system was installed upstream of the air filters, the final barrier filters remain dry and these filters stay cleaner due to the scrubbing effects of the mist. At Las Vegas Cogen, the first cooling stage achieves 7°F of cooling, two stages deliver 12°F and all three provide 15°F. The overall result of fogging is an additional 5 MW of power output.
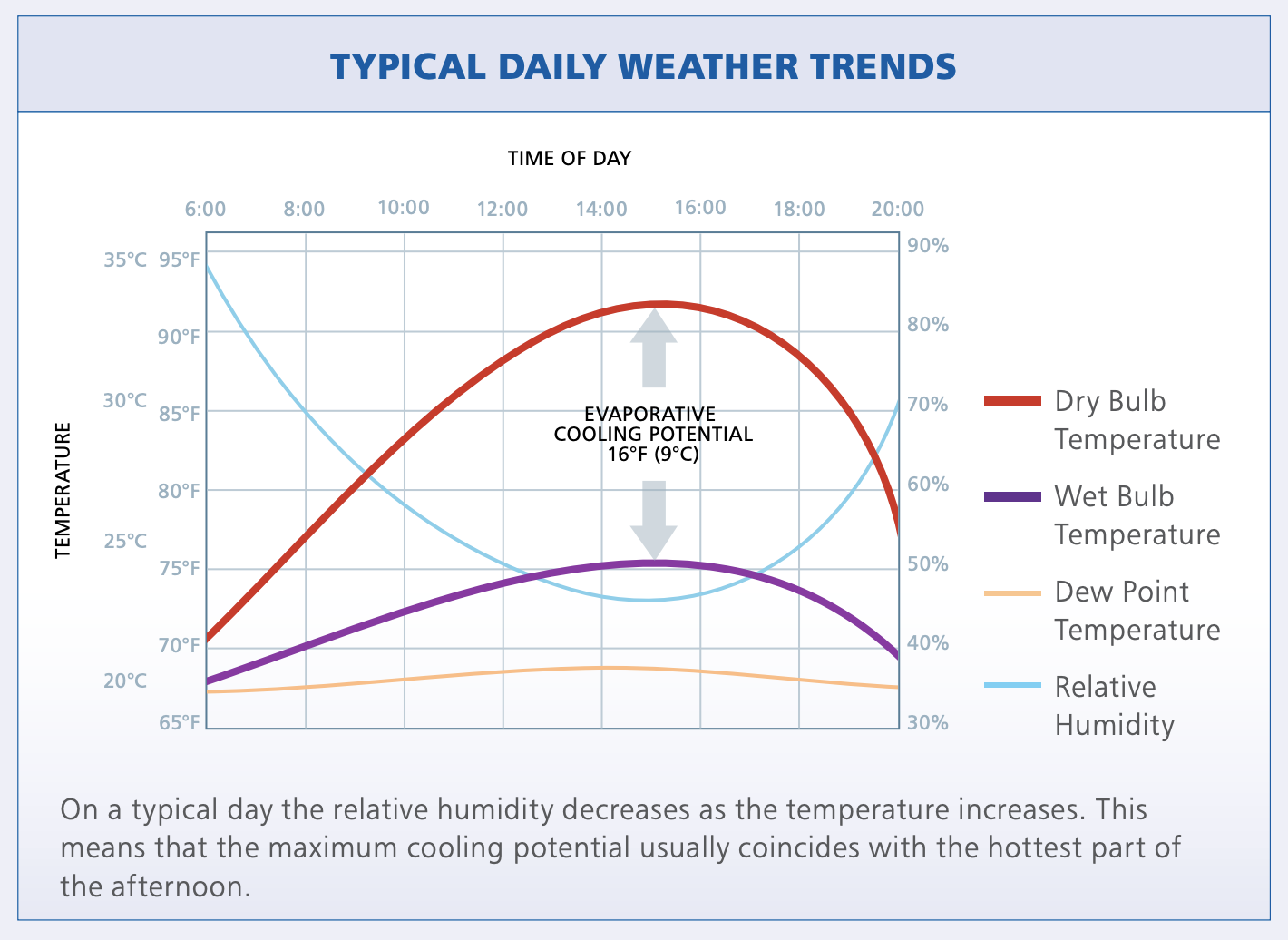
Client Benefits using MeeFog Technology:
• Increased power output by 5 MW
• Lowered energy bills by limiting the use of the chiller system to only high temperature days
• Chiller is enhanced by using fog during the hottest weather
• Installed MeeFog in this configuration without downtime
Due to its low cost, my advice would be to use fog as much as possible. It is simple, reliable and relatively maintenance free. In fact, the fog system has resulted in less operation of our chillers. — RD Dawkins, Operations Supervisor, Las Vegas Cogen
Resources:
Discover how MeeFog Industries’ high-pressure fogging system optimized cooling, reduced chiller usage, and increased power output at the Las Vegas Cogen plant.
Contact Us:
Curious how MeeFog’s high-pressure fogging systems could enhance your plant’s performance and reduce cooling costs?