MeeFog System Enhances Power, Cuts Fuel Usage, and Reduces Emissions at Chinese Compressor Station
Gas Turbine Inlet Air Cooling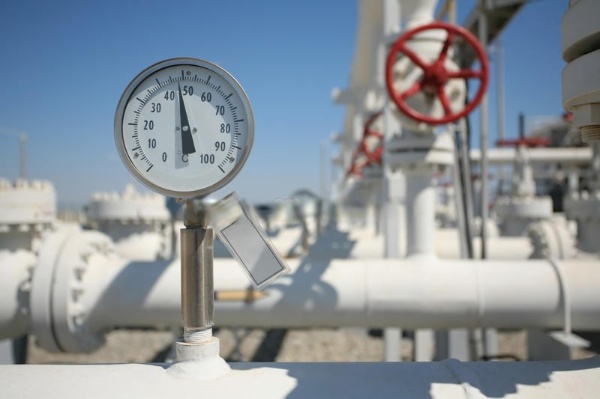
PetroChina
The Lianmuqin compressor station is located near the city of Shanshan in the Turpan Region of Xinjiang Province, Northwestern China. Positioned east of Kyrgyzstan and Kazakhstan, and southwest of Mongolia, the station is critical for transporting gas over thousands of miles to Shanghai and other eastern destinations. The compressor station is situated in a dry region and during the summer, high temperatures reduce compressor output, slowing gas supply to industrial centers in the east.
Challenge:
Due to China’s burgeoning domestic demand for natural gas, PetroChina requires a large number of compressor stations to efficiently push gas along extensive pipelines. High temperatures during summer months cause compressor output to drop, leading to supply shortages and impacting industrial centers in the east.
Solution:
Implement a MeeFog system on a GE LM2500 turbocompressor on China’s Western Pipeline to increase compressor output, reduce fuel consumption and lower NOx emissions, effectively addressing the challenges posed by high temperatures and growing gas demand.
Installation:
The Lianmuqin compressor station consists of three GE LM2500 turbocompressors. As fog systems were new to PetroChina, a MeeFog system was installed in one unit to determine its effectiveness. The MeeFog system consists of a programmable logic controller (PLC), a series of high-pressure pumps, a supply of demineralized water, stainless steel piping, and hundreds of MeeFog nozzles.
Mee Industries utilizes impaction-pin type fog nozzles as droplet size is the single most important factor governing performance. Smaller droplets mean faster and more efficient cooling, minimal wetting of duct surfaces, and greatly reduced water usage. Each MeeFog impaction-pin nozzle is made from high-grade stainless steel. It features a 0.006-inch (150 micrometer) diameter opening which produces billions of ultra-fine droplets per second. The average droplet size is far below 10 microns, or one-tenth the diameter of a single strand of human hair, enabling rapid cooling of the inlet air temperature
The fog system can be controlled granularly from the PLC, with eight stages of cooling available. As temperature rises, each stage comes online providing increasing levels of cooling.
Results:
PetroChina and its local equipment supplier, Circuit Powertek of Shanghai, tested the MeeFog system while the compressor operated at three different compressor speeds:
Speed: 4,505 rpm
- Temperature drop: > 7 °C
- Fuel flow reduction: ~ 3 kg/min
- Turbine power increase: ~ 3 MW
- NOx emissions reduction: 27.4 ppm
Speed: 4,826 rpm
- Temperature drop: ~ 7 °C
- Fuel flow reduction: > 5 kg/min
- Turbine power increase: ~ 3 MW
- NOx emissions reduction: 13.6 ppm
Speed: 5,105 rpm
- Temperature drop: ~ 7 °C
- Fuel flow reduction: > 5 kg/min
- Turbine power increase: ~ 3 MW
- NOx emissions reduction: 8 ppm
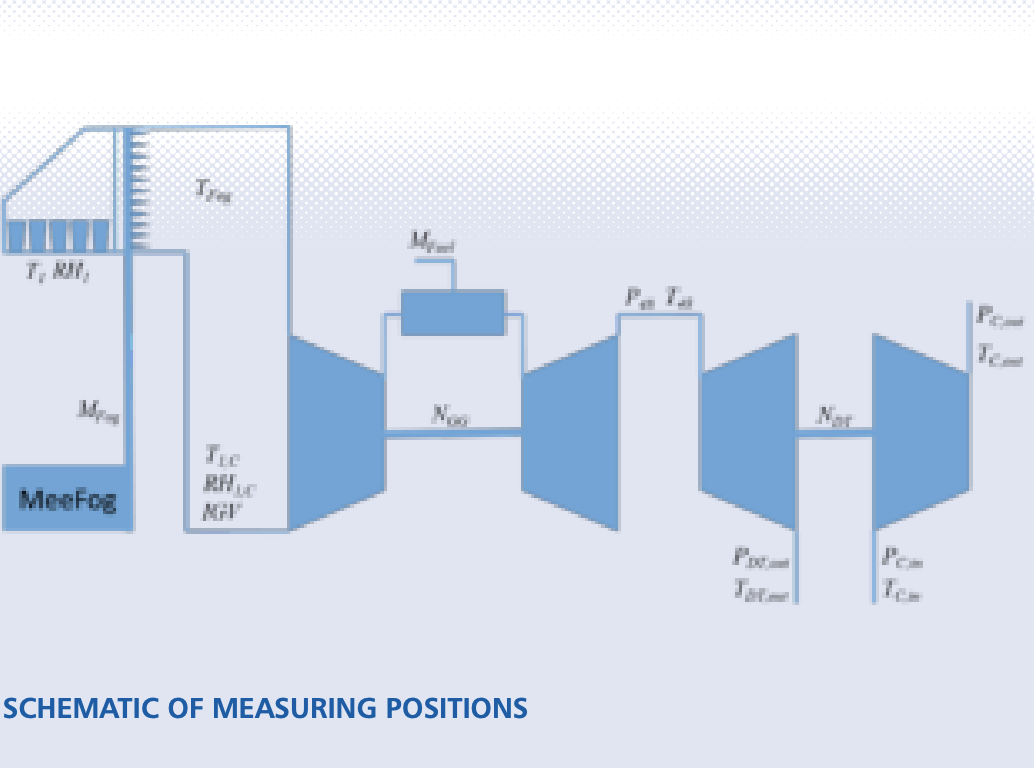
Cost Benefit Analysis:
Additional output: 2.9 MW
Fuel flow reduction: 5.3 kg/minute
NOx emissions reduction: 27.4 ppm
“In summer, the use of the MeeFog system significantly increases output, reduces fuel consumption, and lowers NOx emissions. As the fog system increases output at the station, PetroChina can more easily take one turbine offline and only run two turbines instead of three. This heightens station efficiency and makes equipment maintenance much simpler.” — Xiao Wang, Technical Supervisor, Circuit Powertek
Resources:
Read more about how cooling inlet air produced a significant power boost and improved fuel efficiency.
Contact Us:
Curious about boosting your gas turbine performance? We’ll gladly supply a detailed power recovery report for your existing gas turbines.